您公司是否遇到以下一条或多条类似的问题,如果有其中一条,那么要做品质提升了:
1、 客户经常投诉产品品质问题,维持庞大的管理团队和售后服务部,应对客诉;
2、 产品品质问题多,无法在客户中形成认同,中低档产品代名词;
3、 刚刚做好的产品,又要批量返修,员工怨声载道;
4、 员工只要数量,不要质量,做出来就算了;
5、 维持庞大的检验队伍,防止不良品流出。
品质提升收益:
1、 质量是企业的生命:随着科学技术的进步,市场经济的发展,人们逐渐告别短缺经济。在买方市场条件下,企业间的竞争异常激烈,而竞争的实质是质量竞争,其结果是质量好的企业必将淘汰质量低劣的企业。
2、 质量是企业树立品牌的前提:良好的品牌依赖产品的高质量,没有优质的产品难以树立好的品牌形象,即使品牌形象树立起来了,也只是昙花一现。
3、 质量是企业效益的源泉:一方面,高质量产品与低质量产品相比,生产成本相差无几,但市场上的身价相差可能数倍;另一方面,高质量的生产制造过程降低了废品率和各种消耗,这种低成本的生产过程直接给企业带来经济效益。
4、 质量是市场营销的后盾:高质量的产品给企业的市场营销以十足的信心,是市场营销成功的保证。如果质量上不去,再有成效的市场营销也只能是前面开拓市场,后面丢失阵地,前面扩大销售,后面增加投诉。
品质提升深博套路:
QEP模型:
案例1 广东华雷金属
Before:2015年10-12月份客户需求送货合格率98%,华雷只有94%左右,而且每天都有批量品质事故,每月品质成本占比超过3%,士气低迷,客户投诉频繁,品质成本较高。
After:通过2016年1-3月为期3个月的改善,导入首检、自检、品质变化点管理、品质前三项检讨,应用QC手法对产品进行防呆改善,防呆B/A改善输出26份,送货合格率由96%提升到99.9%,制程合格率由87%提升到98.8% 。
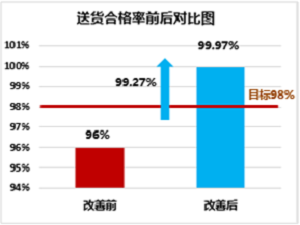
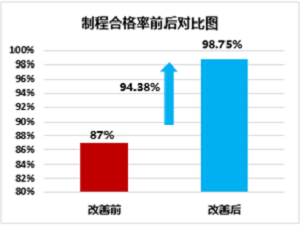
案例2 广东芬尼科技
Before:2015年5-12月份市场客诉率达10%,芬尼科技电控占5%左右,氟路占3%,成品退货返工多,员工埋怨,客户不满意,品质成本较高。
After:通过项目组2016年1-7月为期7个月的改善,导入首检、自检、专检、工艺突破、品质前三项检讨,应用QC手法对产品进行防呆改善,防呆B/A改善输出54份,氟路不良下降73% ,电控不良下降44%。
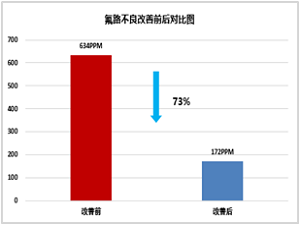
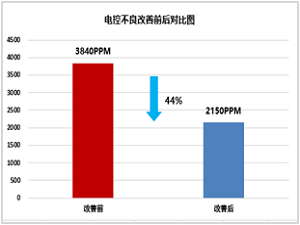
案例3 浙江科博电器
Before: 作为科博电器主要客户,美的、创维、惠而浦、LG、格力、九阳等均为行业领先的企业的,对品质要求异常严苛,而2016年1-6月份科博电器制程品质不良率达22551PPM,导致成品退货返工多,员工埋怨,客户不满意,品质成本较高。
After: 通过2016年6-11月项目组为期6个月的改善,导入首检、自互检、尾数专检、专项突破、品质前三项检讨,QEP手法、客诉流程梳理、供应商帮扶,制程一次不良率由原来的22551PPM下降到10370PPM,下降54%。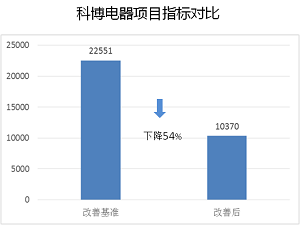